
Ĭompared with chromium, molybdenum has a factor of 1.5 in terms of forming austenite. This concept is best shown in the Schaeffler diagram below and also explained in our ‘ Guide to Duplex and Super Duplex Stainless Steels ‘.
316 stainless steel resistance to chromium chloride series#
However, to maintain the favourable mechanical and physical properties of austenitic stainless steel, any increases in chromium or molybdenum to improve corrosion resistance must be offset by nickel and a series of other elements that act as ‘austenite formers’. Compared with chromium, it is currently about 4 times higher in cost, which offsets the positive factor (3.3) in the PREN calculation. Raising the molybdenum content has a direct impact on an alloy’s cost. So, why is that simple logic not more widely followed?
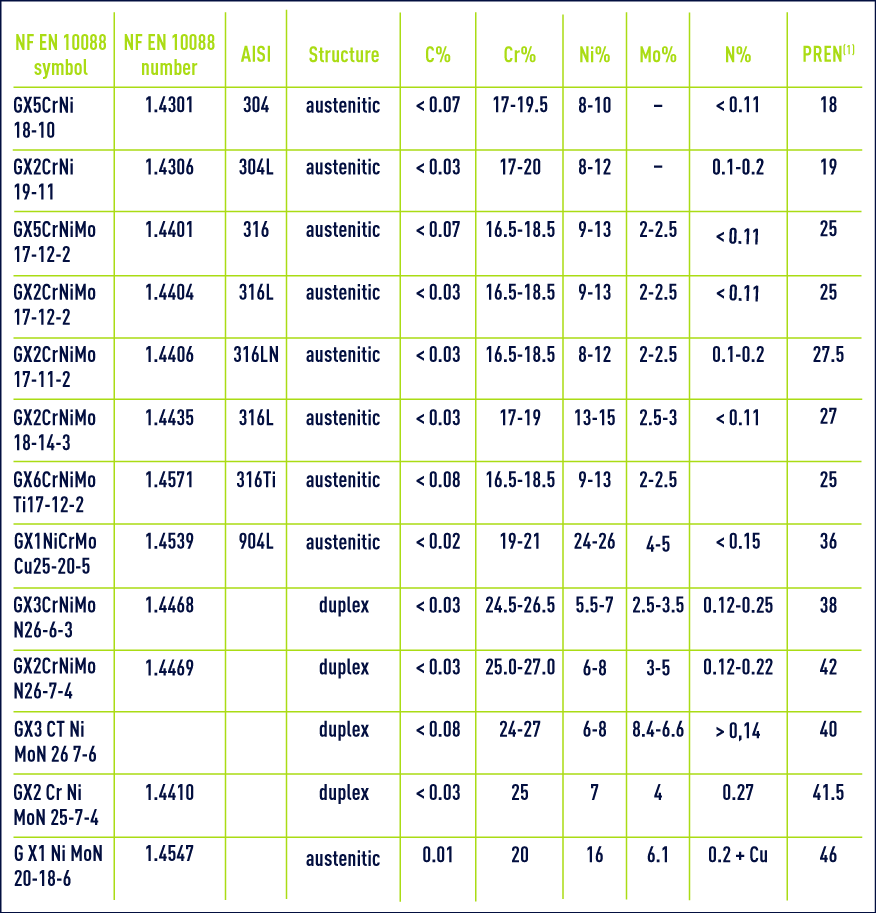
In principle, adding increasing amounts of molybdenum would quickly increase the alloy’s performance. Therefore it can be seen that increasing the molybdenum content results in a greater uplift of pitting corrosion resistance than chromium.
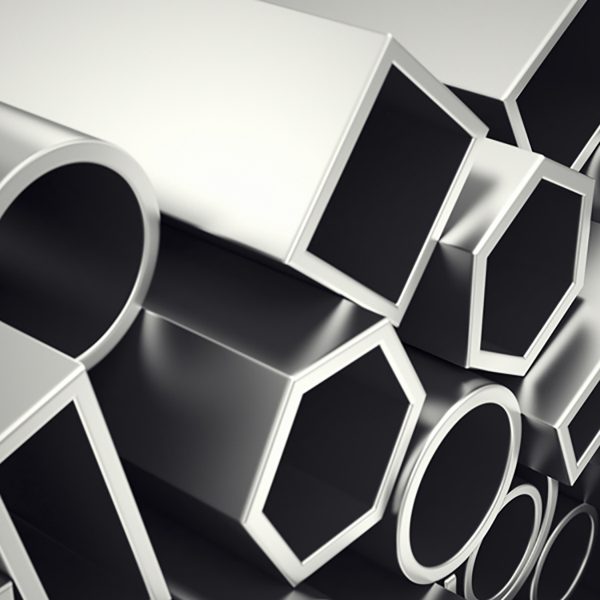
Due to the fact that most product specifications allow a range of compositions, certain end-users will also specify a minimum PREN value to ensure adequate levels of corrosion resistance. The most widely accepted version of the PREN formula utilises the content of chromium, molybdenum and nitrogen as PREN = %Cr + 3.3x %Mo + 16x %N. It is a helpful theoretical way of comparing the pitting corrosion resistance of various types of metals based on their chemical compositions. This PREN value can be used to compare different grades, but cannot be safely used to predict the absolute performance of a grade in a specific application. It is, therefore, a major component in the calculation of the pitting resistance equivalent number – the PREN value. Molybdenum has empirically been shown to improve pitting corrosion resistance. Pitting corrosion is far more likely to occur, where there could be a defect or weakness in the passive film. Increasing the chromium content generally increases the corrosion resistance, associated with a thicker passive film.ĭue to the inherent corrosion resistance of stainless steel, general surface corrosion is rarely a problem. This very thin, self-healing layer provides protection from a wide choice of harsh environments, from seawater to acids, across a range of temperatures.

Above this threshold, it encourages the formation of a highly stable passive film which forms immediately upon exposure to an oxygen-containing environment. What is a Stainless Steel?įor a steel to be considered stainless steel it must contain at least 10.5% chromium. Duplex, super duplex and austenitic stainless steels within Langley Alloy’s stock range all utilise molybdenum in the manufacturing process. Molybdenum is widely understood to improve the resistance to pitting corrosion of stainless steels and therefore is a key alloying element in their composition. The most common application of molybdenum is in the production of stainless steel and nickel-based alloys. The Role of Molybdenum in Improving Corrosion Resistance of Stainless Steel
